Founded in 1923, Laminazione Sottile is the leading Italian Company in the field of rolled aluminium products. With more than 105.000 tons produced in 2017, they cover a wide range of product applications such as packaging, HVAC-R, automotive, cookware and building.
Laminazione Sottile has the ability to supply aluminium coils, sheet, foil and circles in different alloys and widths with gauges ranging from 6 mm down to 6 microns.
On February 2015 the Final Acceptance Certificate of their new MINO Cold Mill was signed by Laminazione Sottile, marking the successful completion of Phase 1 of its long term investment programme in rolling assets.
In 2017 and following the successful completion of Phase 1, MINO received the green light to proceed with the implementation of Phase 2 of the programme, consisting of the design, manufacture and supply of a new Foil Finishing Mill.
The new Foil Mill will be installed in the same Caserta plant and will further add rolling capacity to a long list of equipment supplied by MINO over a 40 year time span:
- one Cold Mill supplied in 1980 and recently refurbished by MINO with new process control system;
- one Foil Roughing Mill supplied in 1983;
- one Hot Mill supplied in 1998;
- the latest Cold Mill commissioned in 2015.
MINO is particularly proud of the long term partnership with Laminazione Sottile, the extent of which now covers nearly 40 years. This relationship is evident by the contract awards given to MINO in hot, cold and foil rolling mills which show a deep level of cooperation and technical trust between the two Companies.
The new Foil Finishing Mill has high-speed rolling potential and will display the latest MINO mill stand design concepts. On-line strip doubling and a number of electro/mechanical solutions allow for tension control at reels over an extremely broad range of material specifications. Complimenting the mill stand are automatic spool transfer devices, a side trimmer and state-of-the-art sensors & instruments.
As with all new MINO mills, the ‘Avanti’ advanced AGC/AFC system controls flatness and thickness of rolled strip. AC motors & drives provide low maintenance, flexible control of speed and torque.
The Mill’s design and automation system is developed in compliance with the Industry 4.0 guidelines, such as advanced process control and monitoring systems, friendly man/machine interface, interactions between different machines, intelligent maintenance system, remote diagnostics. All systems will be designed and supplied by MINO from within MINO’s Automation Division
A key objective within the electrical and automation systems is to achieve high percentage in the Overall Equipment Effectiveness (OEE) levels and to optimise the equipment reliability and operational safety.
The Mill is currently under pre-assembly in MINO’s workshop in Alessandria.
Key data of the new Foil Finishing Mill:
Type of Alloys:
Max. Entry Strip Width:
Max. Entry Strip Thickness:
Min. Exit Strip Thickness:
Max. Coil Weight :
Max. Strip Speed:
AA1XXX, AA3XXX, AA5XXX, AA8XXX Series Alloys
1750 mm
0,6 mm
2 x 0,006 mm
14 t
2250 m/min at Coiler
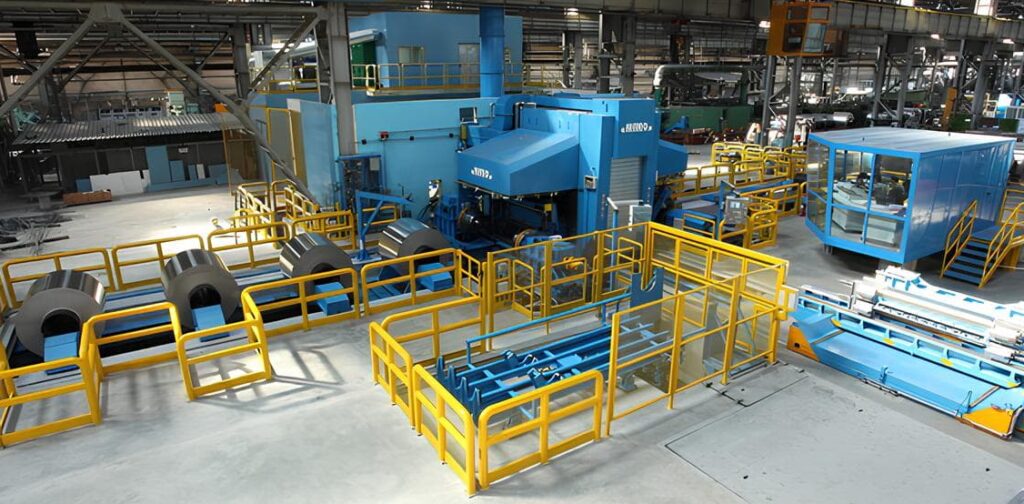