Aluminium
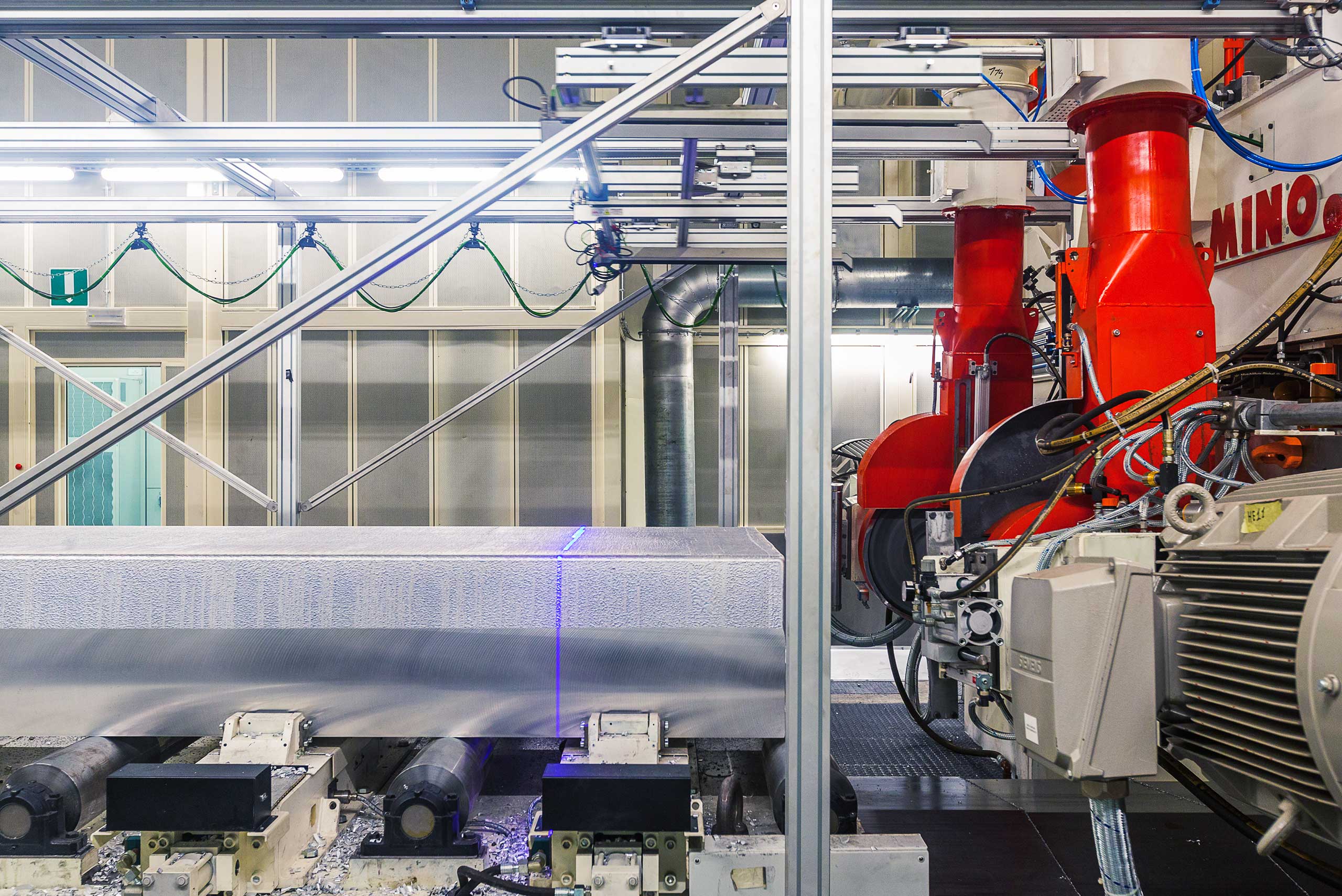
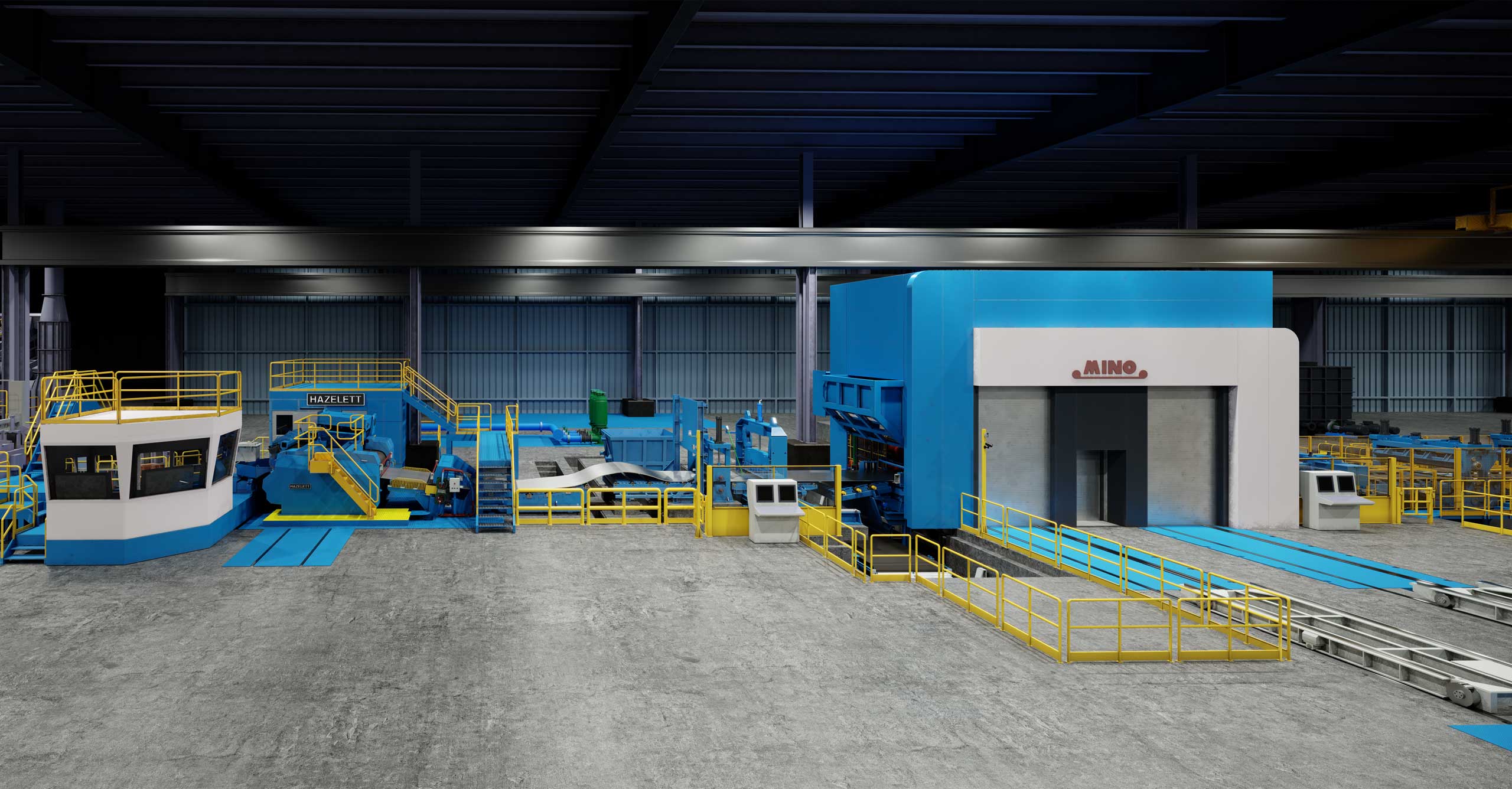
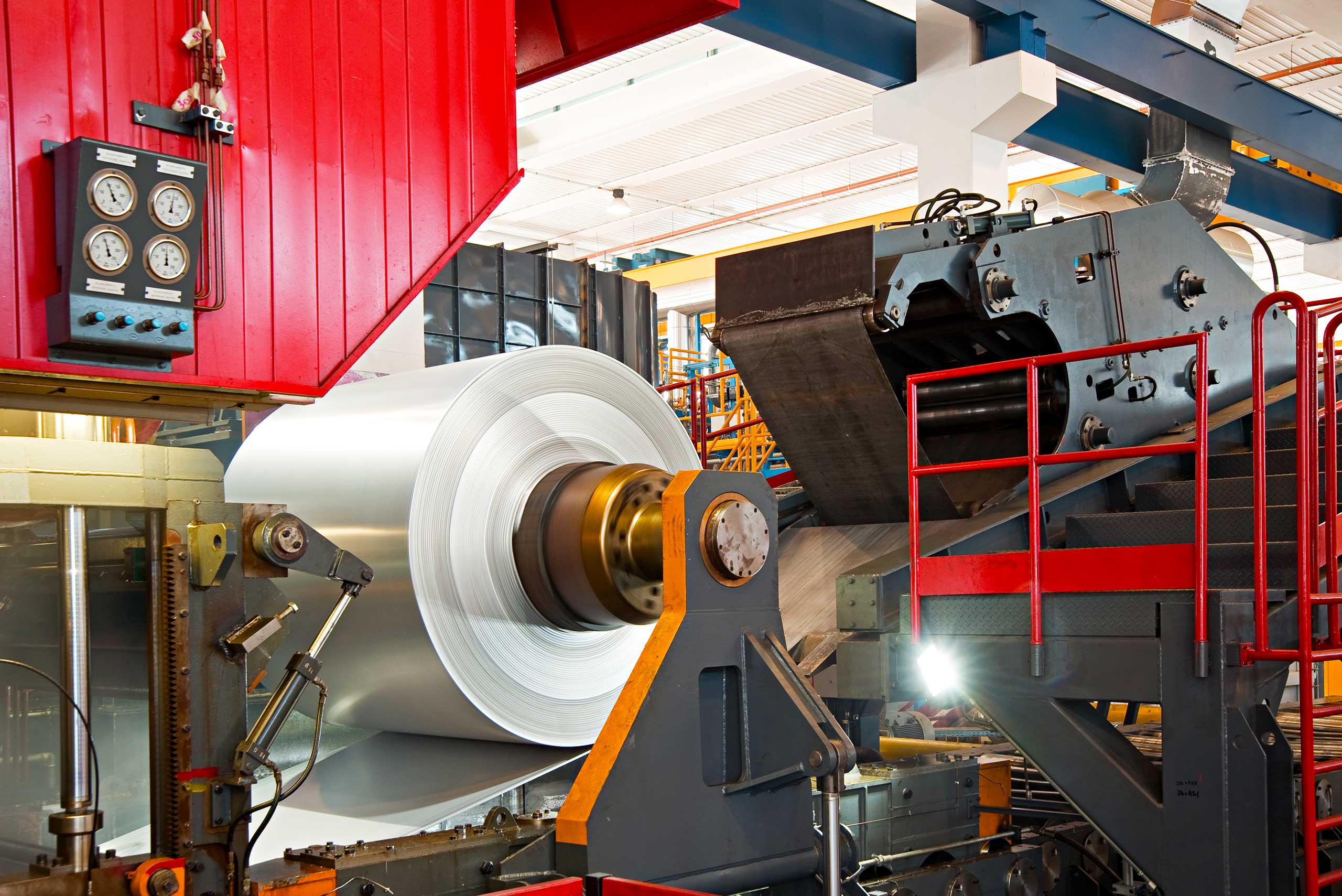
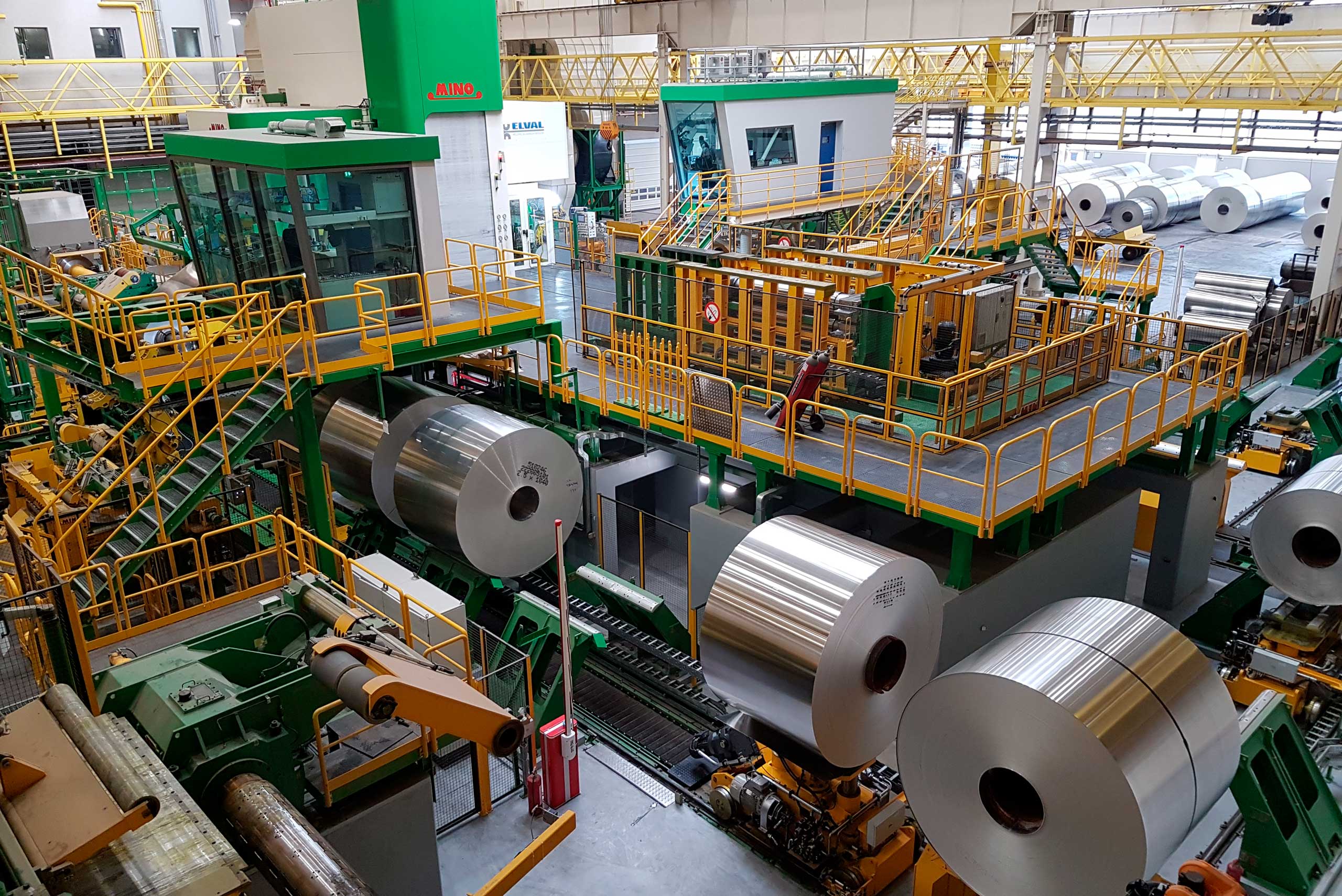
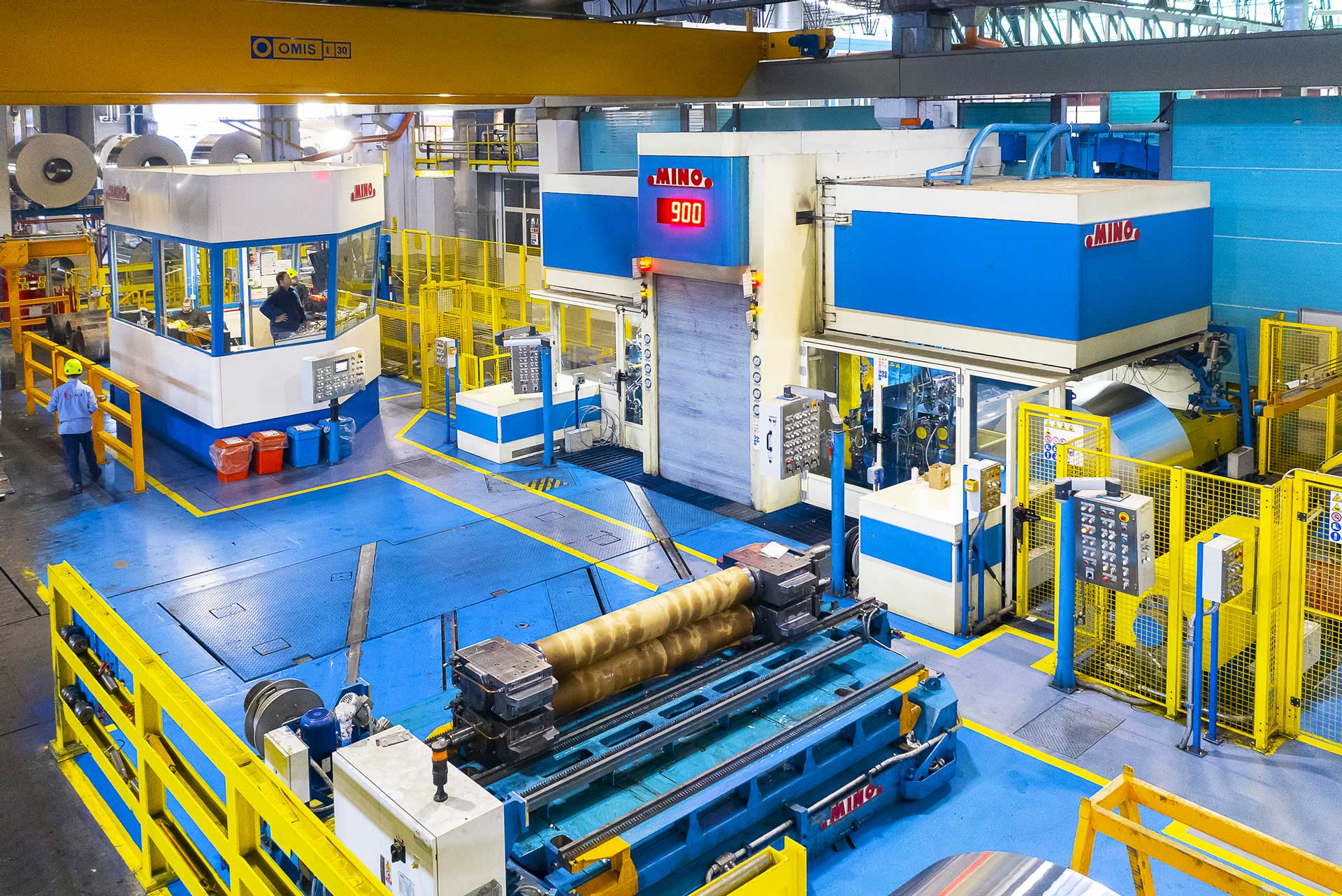
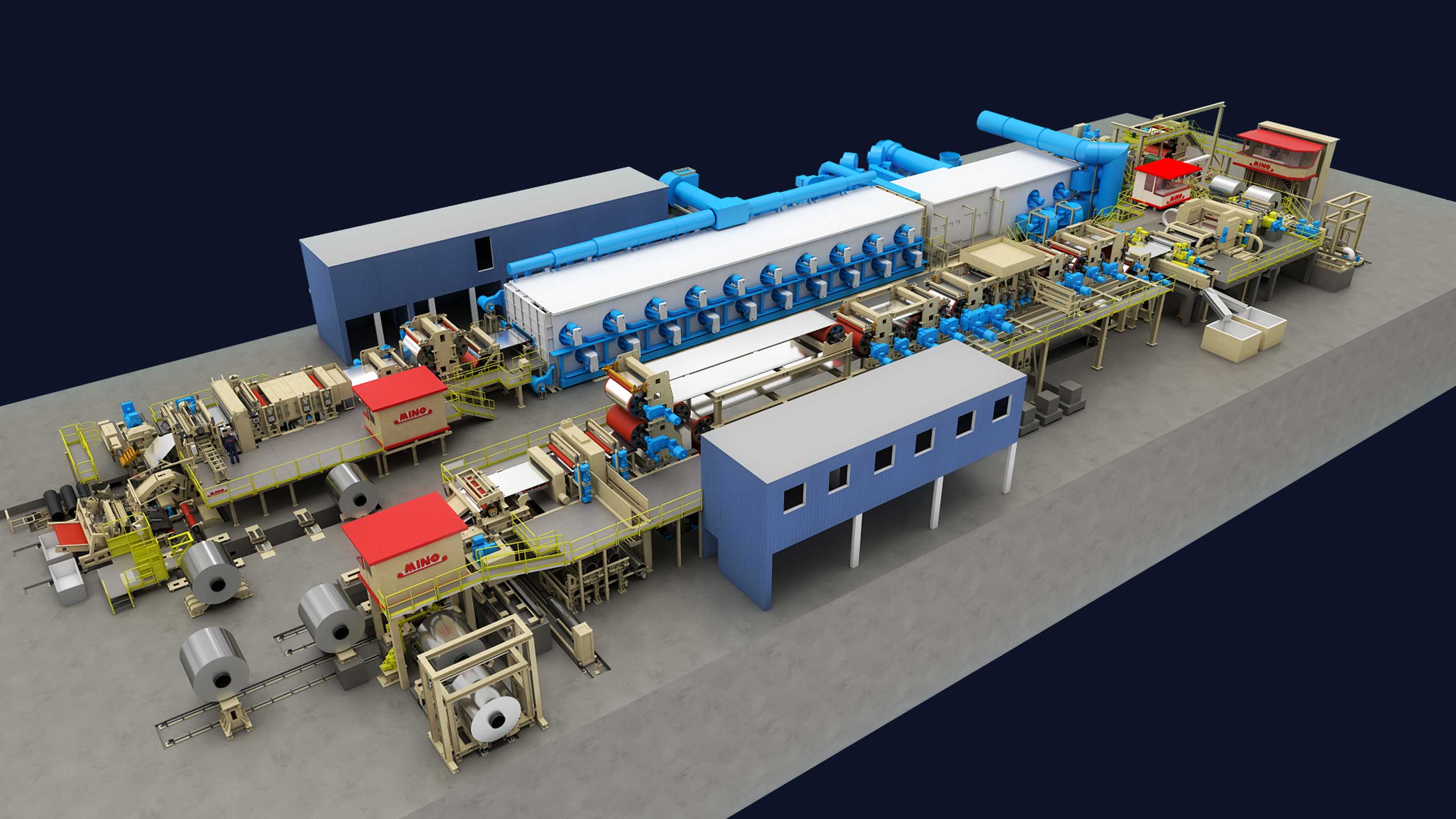
Learn more
Slab Scalping
Learn more
Integrated Melting,
Casting and Rolling
Learn more
Hot Rolling
Learn more
Cold rolling
Learn more
Foil rolling
Learn more
Strip processing
Our strength in Aluminium is the wide-ranging know-how: we can handle from the thickest slab to the thinnest foil strip.
Nicola Gioachin - Managing Director
MINO
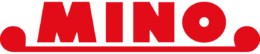

Slab Scalping
Defects in final rolled material necessitate investigation at the upstream stage of the production process, as they often originate from the process which occurs immediately after the casting of the slab: the slab scalping process.
It is now well established that Slab Scalping requires accuracy and consistent, repeatable surface finish and profile.
MINO have designed cutting-edge scalping technology that excels in minimizing scrap removal from while guaranteeing the optimum surface quality.
After comprehensive surface mapping by laser scanning, the scalping heads are precisely calibrated to eliminate the oxidized layer on cast slabs.
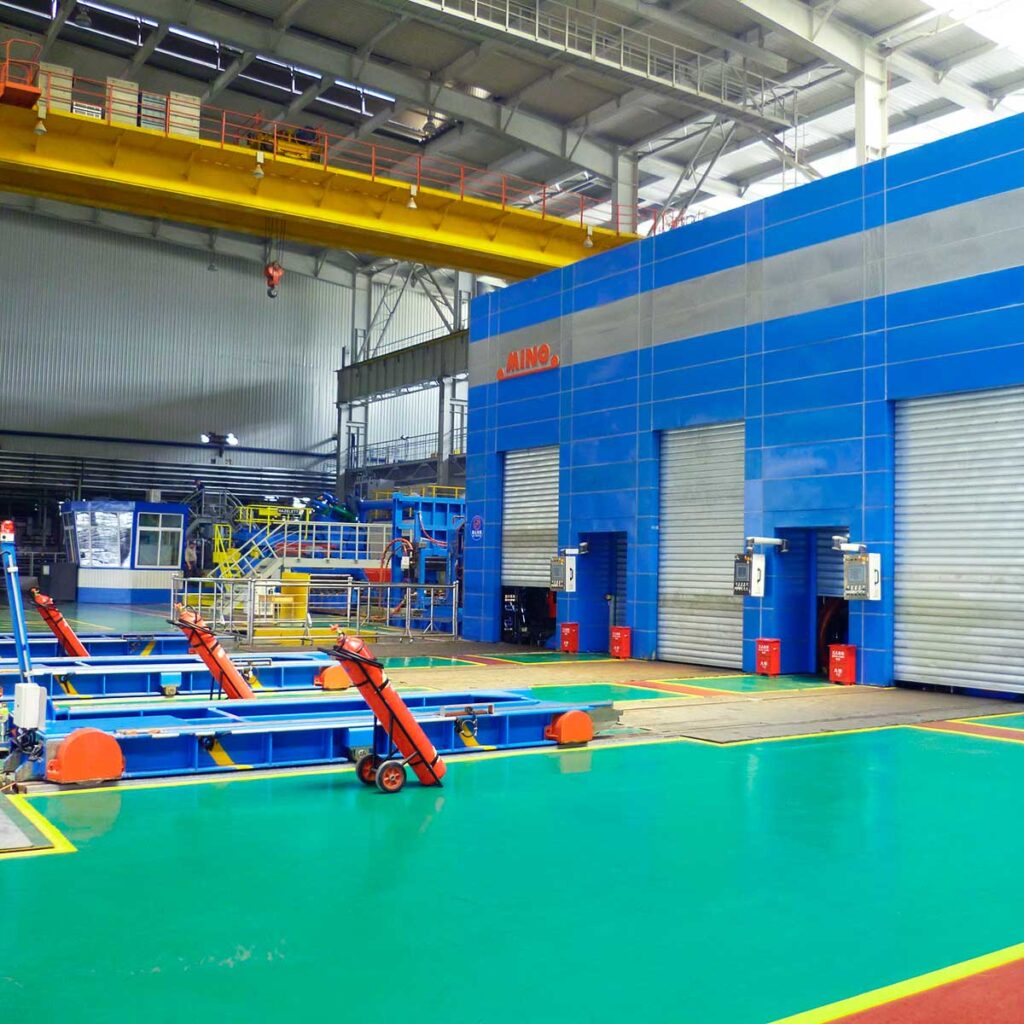
Integrated Melting, Casting and Rolling
Integrated Melting, Casting, and Hot Rolling Lines are a known and accepted process route alternative to traditional Hot Mills fed by slabs.
Since 1997 MINO is cooperating with Hazelett Strip Casting Corp. (located in Colchester, Vermont, USA) on this type of projects and has built up in the years significant references that have become global success stories in the world of rolling.
Our rolling expertise is combined with global equipment brands who partner us to bring a unique process technology to aluminium and non ferrous markets.
EBNER and Hazelett join with MINO to offer a fully integrated aluminum strip Melting, Casting and Hot Rolling Line.
Such production route solution stands out as the obvious choice for reducing energy needs and carbon footprint in the production of aluminum rolled strip.
Besides offering the lowest conversion cost and the most energy efficient process available today in the market for the production af alumium strip, these Lines brings numerous additional advantages to aluminium-semis production, such as the lower capital investment needed for the same output, more compact arrangement, and unbeatable crossing time from liquid aluminium to finished coils ready to undergo subsequent cold rolling.
Such Integrated Melting, Casting and Rolling Lines have the added capability, very unusual in the field of continuous casting, to produce alloys from 1XXX, 3XXX, 5XXX, 6XXX, to 8XXX series providing a wide product range. Finished products include food packaging foil, household foil, fin stock for HVAC, building & construction sheet, deep drawing applications, medium-strength sheet suitable for truck trailer, 5XXX automotive applications, 6XXX for containers applications.
Additionally, such Integrated Melting, Casting and Rolling Lines can cast and hot-roll strip widths up to 2 meters wide, at an hourly production rate of 50 Metric tonnes per hour.
In summary, such an Integrated Melting, Casting and Rolling Line is a decisive step toward a more productive and environmentally sustainable process for the future aluminum industry, without any compromise on production flexibility (in terms of variety of alloys), or in produced quality.
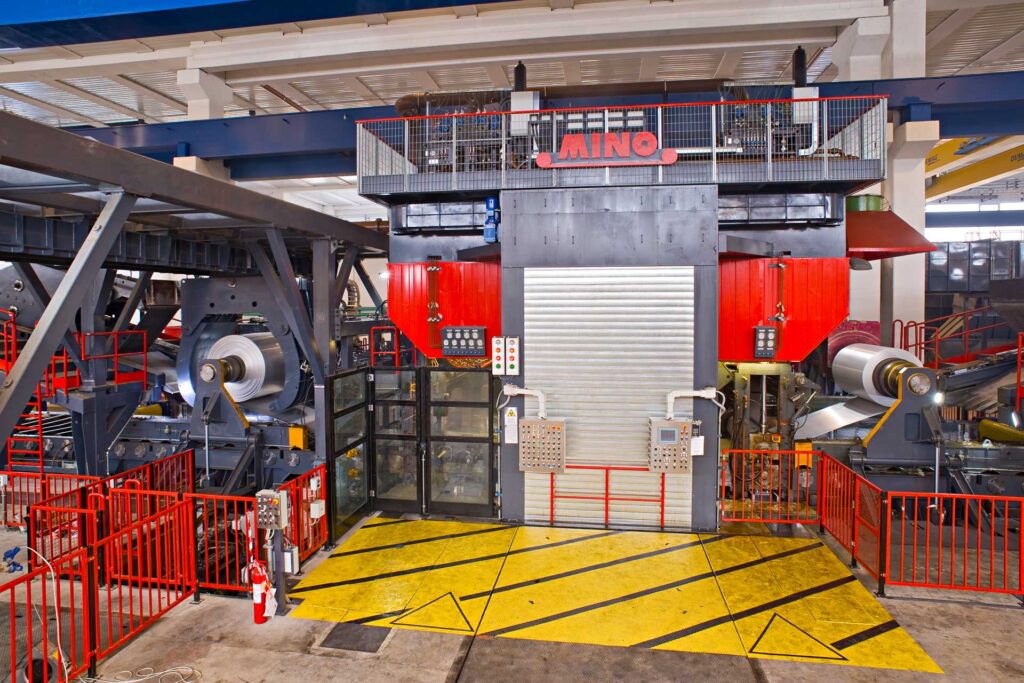
Hot Rolling
MINO’s first single stand Hot Mill was delivered and installed in the early 1960s, first Hot Tandem Mill was delivered and installed in the early 1980s and since that time we have designed and built Single Stand Reversing and Tandem Hot Mills in various configurations.
Our references include configurations from single stand reversing to the more complex and flexible 1 + 1 (one roughing stand and one finishing stand, where the last 2 to 4 passes are performed), to the highly productive 1 + 4 multi stand Hot Mill.
All MINO’s Hot Rolling Mills provide high quality hot rolled strip with the flexibility to produce products for all alloy ranges.
Complexity of design and control will depend on the product demand required.
MINO design and build in-house its own control for all our Hot Mills which guarantees thickness and profile control to highest market requirements.
In today’s demanding marketplace, our clients expect to be provided with automated mills which allow continuous and consistent quality levels day in, day out.
MINO strives for Continuous Technological Advancements, enhancing both the productivity and reliability of its equipment’s key components.
Auxiliary equipment (such as the cooling system with annexed emulsion filters) are also critical to success, hence a sophisticated blend of mechanical design, advanced automation, effective cooling/filtration systems provide essential reliability and quality to the package.
Our own in-house Process Control incorporates Self-Learning Models for stand presetting and slab profile control, allowing the complete supply of a state-of-the-art Hot Rolling Mill sourced from one single supplier… MINO.
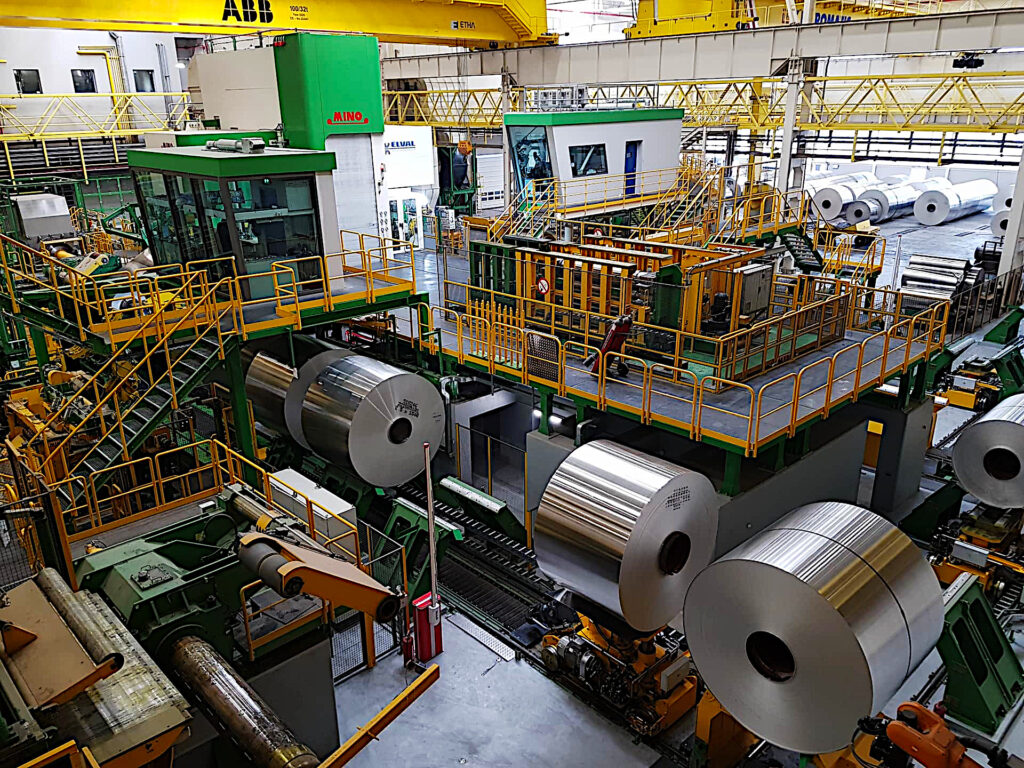
Cold Rolling
Cold rolling adds value to the client’s production, with material supplied either from a MINO’s Hot Mill or an Integrated Melting, Casting and Rolling Line.
Drawing from decades of expertise in cold rolling design and build (first Cold Mill working “in coils” was commissioned in the early 1950s) MINO has established a sound & global reputation for excellence, backed by a long list of successful references around the globe.
Whether you require a Six-high Cold Mill or a multi-stand Tandem Mill, MINO has the capability to supply proven designs.
All our Cold Mills come with MINO ‘AVANTI’ integrated package of automation and process control.
All MINO’s Cold Mills are tailor-made to client’s precise requirements, including special productions/applications (such as Can Stock, Automotive or Aerospace) and specific lay-out arrangements to fit in the available space.
Starting from the conceptual/design phase, the mechanical and hydraulic components of MINO’s Cold Mills are seamlessly integrated with the automation system, ensuring perfect thickness & flatness results and optimal productivity during the cold rolling process.
Our state-of-the-art mathematical models allow the Cold Mill to automatically adjust its starting parameters with each pass, continuously refining the rolling process.
Well-conceived, fully automatic coil and spool handling systems are installed to minimize the idle coil-to-coil time and boost productivity.
Moreover, several optional features can be offered to complete the Cold Mill’s configuration, such as different EDT/skin-pass rolling capability, hot edge system, coil preparation, coil inspection and/or coil finishing.
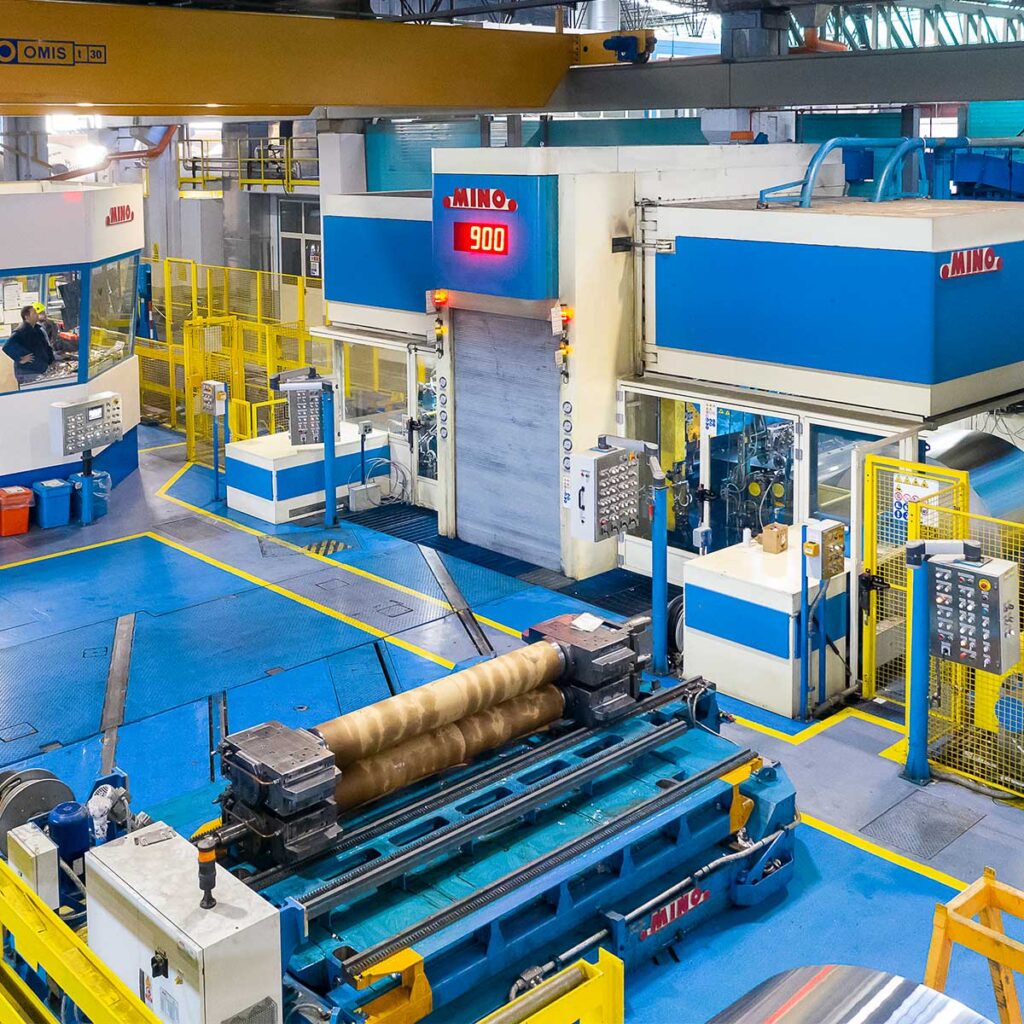
Foil Rolling
Thin gauge material is widely used in food packaging, pharma, electronics and now in the production of lithium-ion EV batteries.
Our clients expect the highest quality of design to achieve and satisfy their demands.
Hence the Foil Mill and its auxiliary equipment must perform to a consistent and constant level 24/7.
MINO built its first Foil Mill which went into production in the 1970’s and has, ever since, refined its mechanical design and its process control system.
After that first supply of a Foil Mill and during the following years to date, MINO has remained at the cutting edge of thin gauge rolling mill technology and development.
Foil Mill’s design demands an almost watch-like precision and extreme attention to the tiniest detail; hence all MINO’s Foil Mills are designed, built and pre-assembled in our workshop with this in mind, ensuring that foil industry gets what it needs.
Moreover, top-notch Process Control System is installed, ensuring best thickness and flatness control and optimal speed rump-ups.
Our comprehensive Foil Mill portfolio encompasses Universal, Intermediate and Finishing Foil Mills, as well as specialized Battery Foil Mills for the production of 10-12 µm “single leaf”, bright/bright foil, with optimal surface wettability values.
Spanning all strip widths, we provide Foil Mills in the range from 1250 mm to 2300 mm.
In the world where ultra-thin gauges are necessary, MINO has proven designs and references with many world class clients.
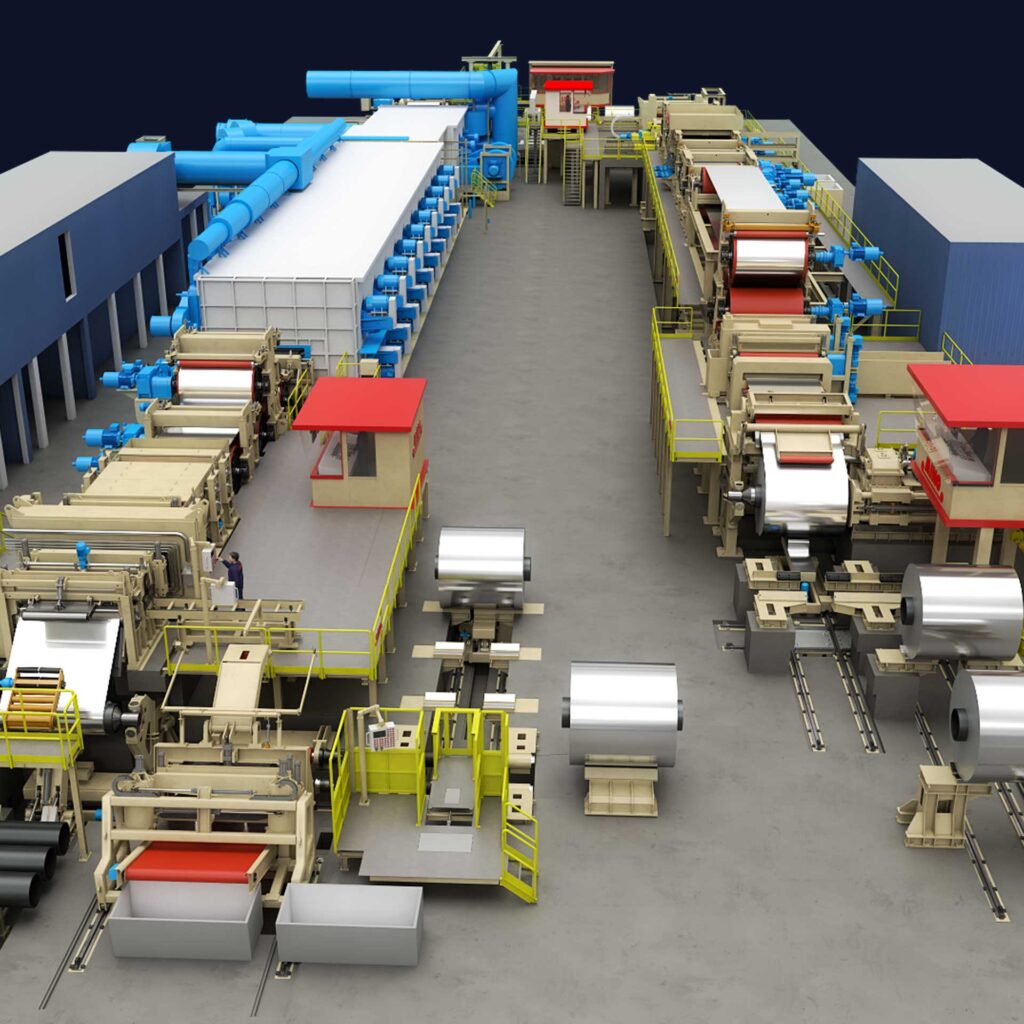
Strip Processing
As a complement to Cold Rolling, MINO has the capability and expertise to supply Strip Processing Lines for the finishing of the cold rolled strip, including ‘Annealing & Heat Treatment Lines‘ and ‘Tension Levelling, Cleaning & Passivation Lines‘, specifically designed for Automotive applications.
Annealing & Heat Treatment Lines include floating furnace and quenching section supplied by the thermal equipment specialist and incorporated in the MINO’s Line to allow continuous process of 5XXX and 6XXX series alloys.
In particular, in the case of 6XXX alloys, the Annealing & Heat Treatment Line allows to realize the solution heat treatment, quenching and age hardening of the strip, making it suitable for Automotive outer-body applications.
A separate Tension Leveling Cleaning & Passivation Line will improve the flatness, clean and passivate the strip, as required by the final customer.
Both Lines are designed for continuous/endless operation, being equipped with stitcher/welder, entry/exit accumulators and double decoiling/coiling equipment.
A skin-pass stand can be incorporated in the line, for providing specific roughness to the strip using specially textured work rolls.
The high roughness surface increases the formability of the strip in the subsequent deformation process, by lowering its friction coefficient thanks to the lubrication “pockets”.
With the addition in MINO’s portfolio of such finishing lines, MINO achieves the unique and enviable position of being capable of providing the complete equipment chain of slab scalper, hot rolling mill, cold rolling mill and finishing lines for Automotive applications.
MINO, using exclusively its equipment and cooperating with the thermal equipment specialist, is in position to take a casted slab of aluminium alloy and transform it into a rolled, heat treated & finished strip, covering all automotive aluminium sheet applications, from inner structure to outer panels.