Copper
Many can roll copper down to 25 µm, reaching 6 µm is for the few.
Geminiano Chiesa - Proposal Manager
MINO
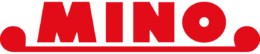
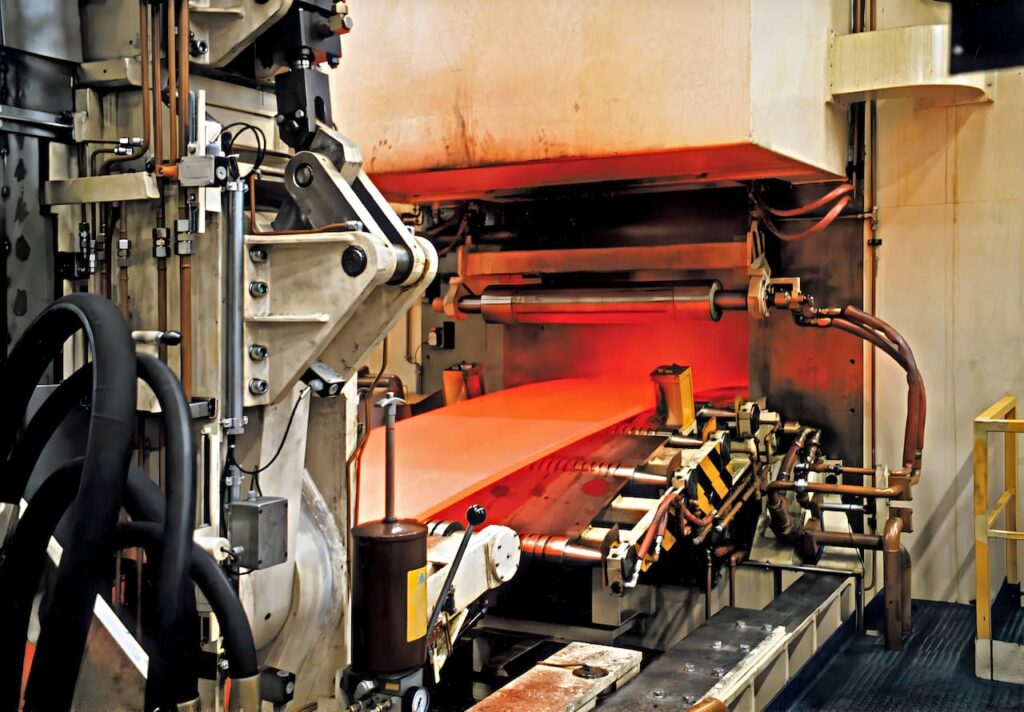
Hot Rolling
MINO Hot Rolling Mills for copper provide the traditional starting point in a rolling plant for copper and copper alloy flat products.
Having supplied its first Hot Mill for copper back in the 1950s, MINO’s design is based upon decades of experience and cumulated know how.
A modern Hot Mill is the keystone of a copper flat products plant, as it governs thickness and determines the metallurgical structure of the downstream products.
Hot rolled strips are suitable for the most demanding industry applications, including ultra-thin copper foil production.
A modern Hot Rolling Mill for copper and copper alloys is supplied today complete with a powerful edger and efficient descaling equipment.
The outgoing strip can be either supplied flat after being cooled in a cooling tunnel (ready to undergo milling) or coiled at the end of the line.
While, typically, Hot Mills for copper strip are of two-high design, it is noteworthy that MINO has supplied the only Four-high Hot Mill running in the world.
The subject Hot Mill is coupled to a continuous Hazelett belt caster and produces 1250 mm wide copper strip with exceptional metallurgical characteristics.
Precision engineering and bespoke design are essential to meet the specific applications of the hot rolled strip and today’s market requirements.
A MINO Hot Rolling Mill for copper and copper alloy flat products defines rolling excellence in the reference sector.
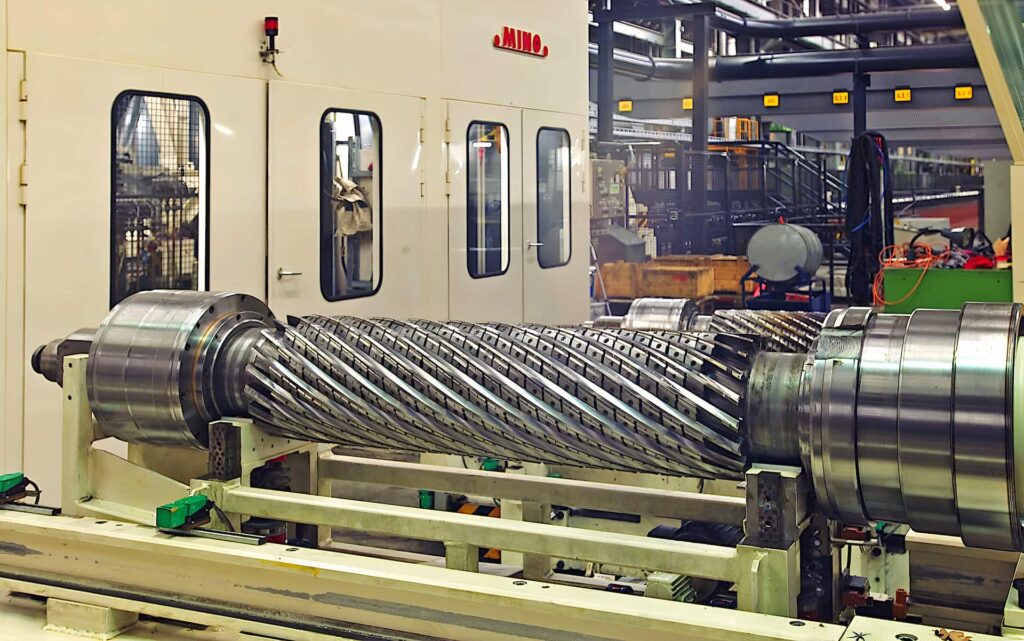
Milling
After hot rolling, it is of paramount importance that strip milling is performed well with the aim of removing the oxide film from all surfaces (including the edges), of improving strip’s crown and of equalizing strip’s longitudinal thickness.
MINO Milling Lines are renowned for their performances and quality level achieved in the outgoing milled strip of copper and copper alloys.
These Milling Lines excel in not only removing oxide film from all strip surfaces, but also in equalizing strip’s thickness and in shaping the strip’s section profile with consistency.
Controlling accurately the milled depth and removing effectively all chips produced in the process are the key challenges of the milling process.
Achieving this level of performance relies on well designed and vibration-free mechanics, combined with a top-level automation system which controls accurately the milling thickness.
Besides precision cutters and advanced process automation, a state-of-the-art MINO Milling Line is equipped with brushing devices, quick cutter changing device, deburring device and efficient chip’s suction system.
Exit skin-pass mill and different types of coilers are offered, including mandrel-type coilers that can coil the milled strip under tension with excellent coiling quality.
New design in cutter-bearings assembly, new advanced systems ensuring “zero-backlash” operations and increases in the cutters’ rotation speed have been among the latest MINO’s developments in this specific field.
With a MINO Milling Line clients are ensured a superior equipment combining high performance and long-lasting operation.
Our Milling Lines represent the industry’s standard in the field of copper and copper alloys strip, providing consistent quality on outgoing strip and trouble-free operation in the milling process.
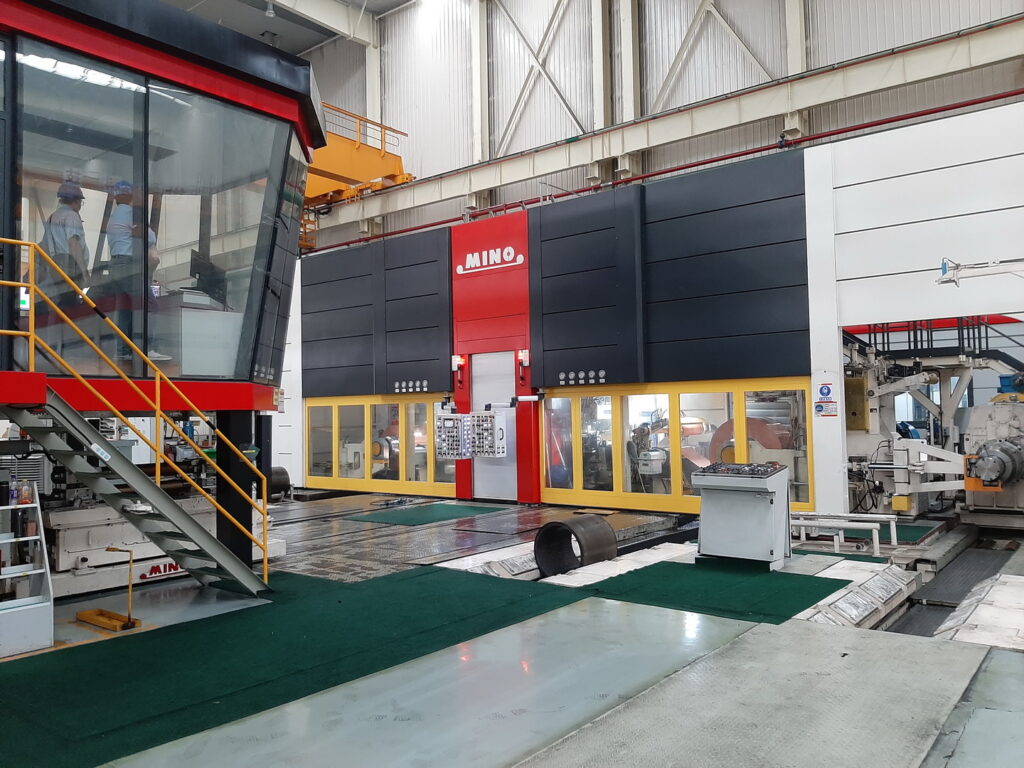
Cold Rolling
The Cold Rolling of copper and copper alloy strips must encompass an extremely broad spectrum of materials, thicknesses and final applications, ranging from thick brass strip down to thing gauge copper for electronic applications.
MINO has developed in the years very diverse and optimized designs of Cold Rolling Mills for coping with such diverse requests coming from the market.
Having supplied its first Cold Mill for copper back in the 1950s, MINO’s different designs are based upon decades of experience and extensive know how.
The large family of Cold Mills for copper and copper alloy strips subdivides in Cold Roughing Mills (from as-milled down to rough-rolled thicknesses) and Cold Finishing Mills, rolling the strip down to final thicknesses for the specific applications.
Strip thickness can be further rolled down to ultra-thin foil gauges by using one more type of Cold Mill, Foil Mills.
Today MINO holds a world class position in the market of Cold Rolling Mills for copper and copper alloy strips.
MINO’s continuous push in innovating and optimizing its design enables our clients to benefit from the best designs available in the marketplace today, tailored for the specific application.
Clients awarding MINO with repeat orders during the years, are a clear testament to this.
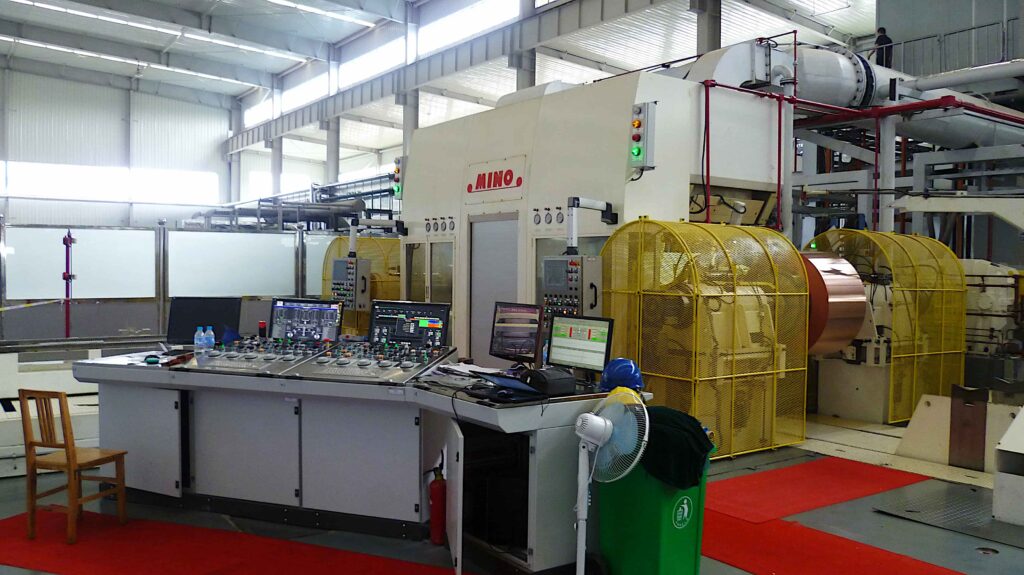
Foil Rolling
Copper Foil Rolling Mills represents the ultimate frontier in cold rolling of copper strip for advanced applications, such as PCB (Printed Circuit Board), anode for lithium-ion EV batteries, heat exchangers, electric connectors or cable shielding.
MINO have pioneered and mastered this technology and have unique solutions for producing copper foil as thin as 6 µm (that is 0.006 mm, not to be forgotten that the average diameter of a hair is 20 µm!).
Such result is even more impressive when considering that, unlike aluminium foil that can be rolled “doubled”, copper foil must be rolled as “single-leaf” to avoid welding together of the two strips.
Handling of such strip thickness implies highest level of tension/speed control ever achieved in the metal sector.
The industrial production of 6 µm rolled strip is made possible by a unique combination of multi-roll mechanical design and state of the art controls.
Our process automation systems AVANTI ensures unwavering precision when rolling such exceptional thin products, guaranteeing best-in-class tension/speed control.
Our cutting-edge MINO Copper Foil Mill is of proven design.
Already with over a decade in copper foil production, this uniquely engineered Foil Mill enables clients to reach levels of thickness rarely seen in modern market arenas.
The single-leaf rolling process is achieved with a maximum strip width of 670 mm.
MINO pushes the boundaries of copper foil production and today still advances the technology further than the competition.
We remain at the forefront of the copper rolling process, delivering unrivaled performance and innovation.