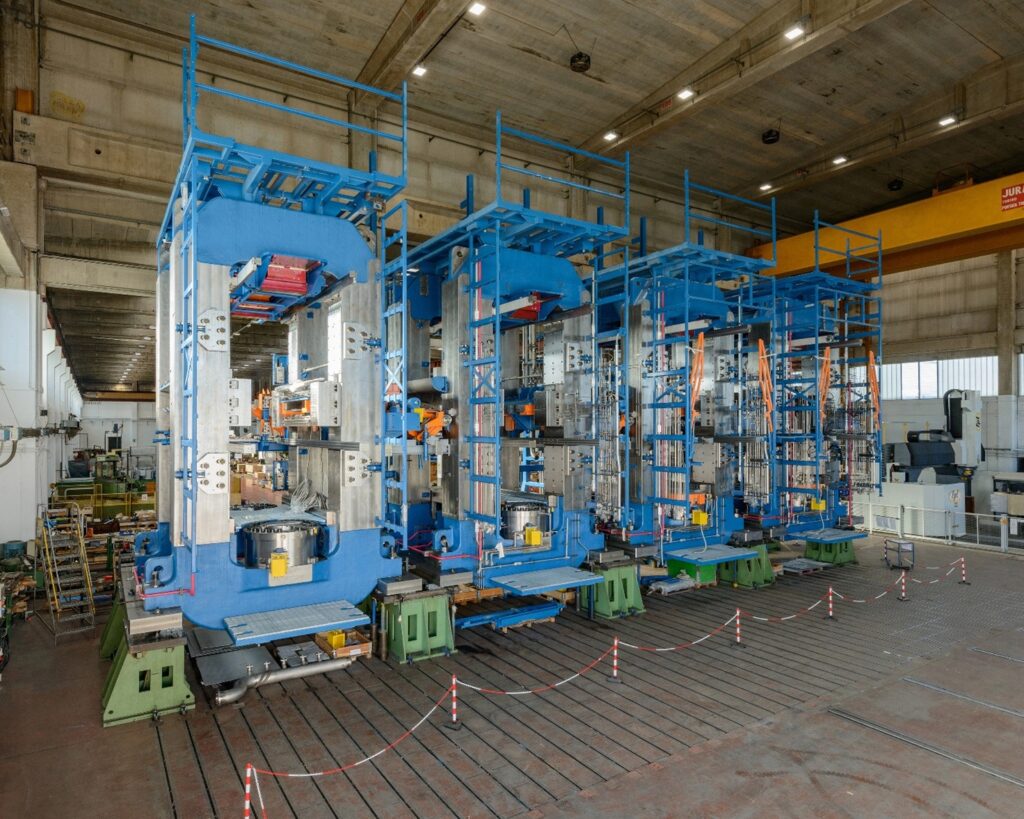
MINO is proud to announce the completion of the mechanical manufacturing and pre-assembly of a state-of-the-art Four-stand Hot Tandem Mill for an undisclosed North American customer.
This advanced equipment represents the pinnacle of hot rolling technology, offering unmatched performance in hot finishing of aluminum-alloy strip.
Designed to process rough-hot rolled aluminum-alloy bars with entry gauges of 20–40 mm down to final gauges as thin as 2.0 mm, the Hot Tandem Mill delivers exceptional output, precision, and quality. It ensures outstanding thickness tolerances, profile accuracy, surface finish, and metallurgical integrity, supporting a wide range of applications, including
- Common alloys
- Automotive components
- Can-stock
- Foil-stock
- Transportation
- Aerospace
A great achievement in pre-assembly
The Hot Tandem Mill has reached a chief project milestone: completion of pre-assembly at MINO’s workshop in Alessandria, Italy. The equipment is a stunning sight in MINO’s heavy pre-assembly bay, served by a 150-ton overhead crane. Pre-assembled with all on-board piping, sensors, and cabling, the Hot Tandem Mill reflects MINO’s commitment to quality manufacturing and to smooth and fast site installation.
Technical Highlights
The Four-stand Hot Tandem Mill for Aluminium coils is engineered for exceptional performance, featuring:
- Maximum strip width: 1,800 mm
- Minimum gauge: 2.0 mm (soft alloys), 3.5 mm (hard alloys)
- Rolling force per stand: 3,500 tons
- Installed power per stand: 5,000 kW
- Cooling system: fully independent, optimized for hot finishing rolling with a flow rate of 36,000 l/min
- Edge trimming: Side trimmer and scrap chopper included
- Advanced process control: AGC system and profile measurement and control
- State-of-the-art AC drives: medium voltage, synchronous motors
Unparalleled Scale and Engineering Excellence
The Hot Tandem Mill displays engineering on a grand scale:
- Each of the eight cast steel housings weighs 115 tons.
- The gearboxes for stands 1 and 2 weigh 130 tons and 100 tons, respectively.
- The mechanical assembly alone reaches nearly 2,000 tons.
- The total weight of the supply, including hydraulics, cooling, electrics, and instrumentation, exceeds 3,000 tons.
Transporting this massive equipment required 200 containers and 80 cases, making the logistics a project in itself.
Gearboxes: precision engineered and pre-tested
The gearboxes have been designed by MINO’s technical specialists and its components have been fabricated by specialized suppliers in northern Italy. All the parts have been assembled, completed with lubrication systems, and rotation-tested in MINO’s gear-boxes testing station, located in MINO’s Alessandria workshop. After testing, the gear boxes have been accurately packed for ocean transportation and shipped in a fully pre-assembled state.
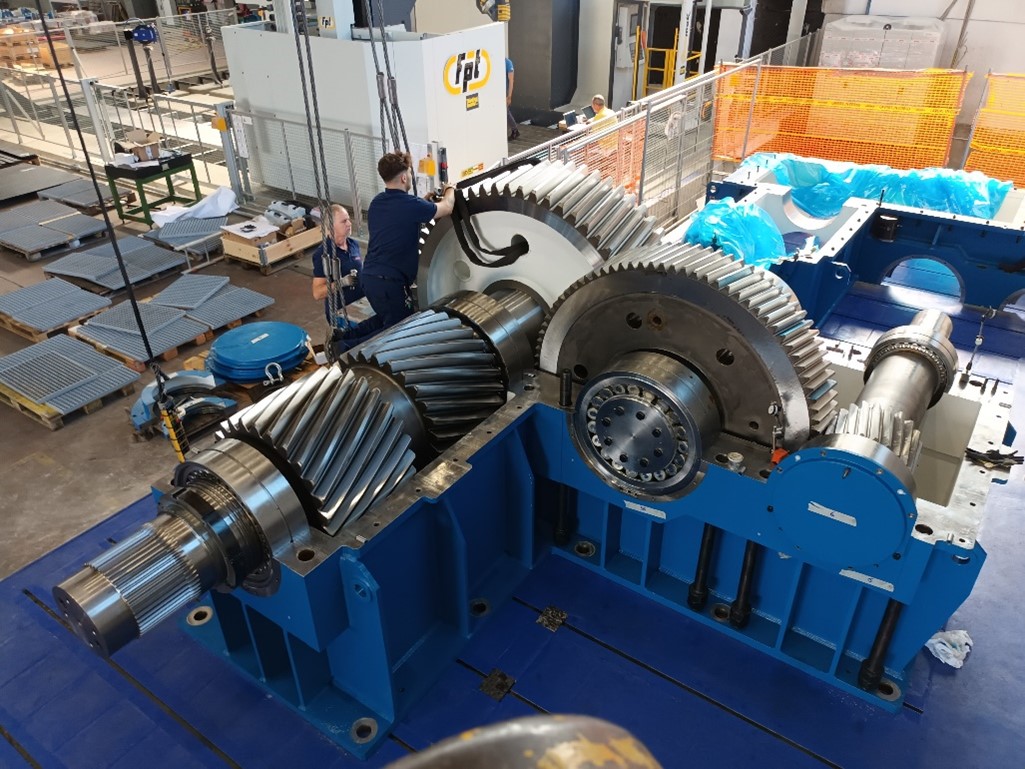
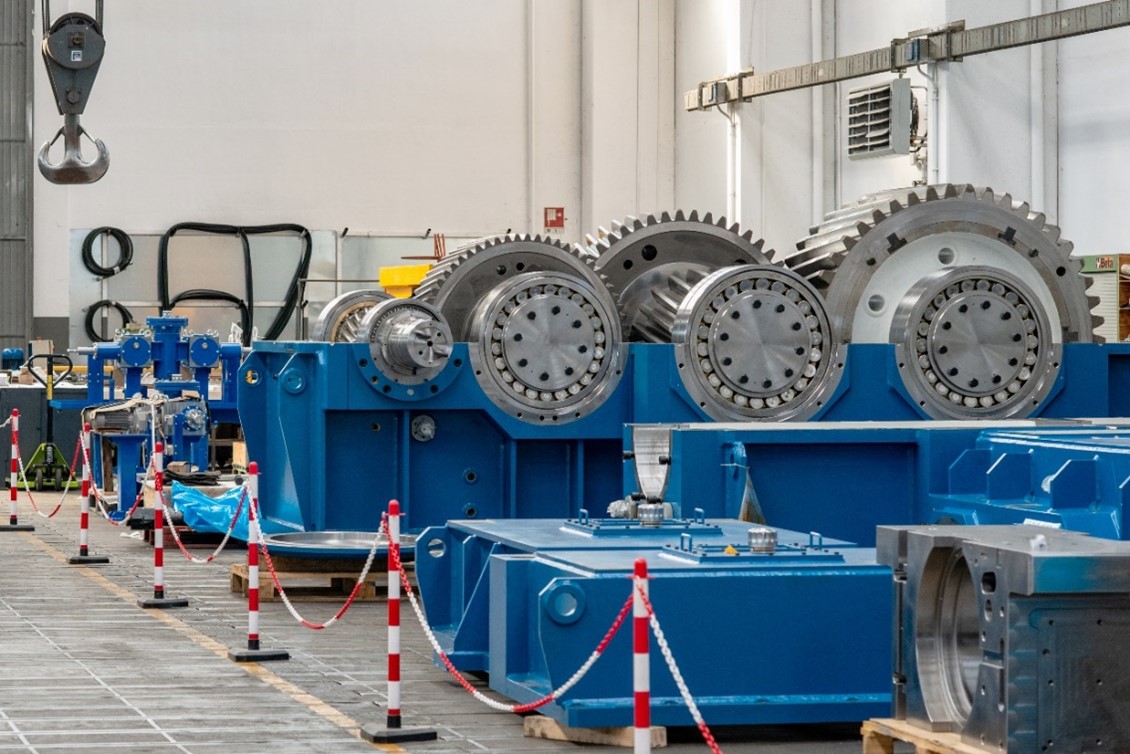
Advanced automation: Self-learning Model-Based L2 System
The Hot Tandem Mill is equipped with MINO’s advanced Self-learning Model-Based L2 System, developed in collaboration with CSM (Centro Sviluppo Materiali, a Rome-based metallurgy research institute). This sophisticated system collects and analyzes large volumes of data through sensors installed along the line. It continuously optimizes thickness, strip profile, and final coil temperature through iterative self-learning processes.
Successfully installed in several projects in Italy, China, South Korea, and the US, this system ensures industry-leading performance and adaptability.
A commitment to excellence
The completion of pre-assembly marks a significant milestone in this valuable project.
MINO is honored to deliver this cutting-edge equipment to our North American customer, reinforcing our reputation for innovation, quality, and reliability in the global metals industry.
Stay tuned for further updates as the project progresses into installation and commissioning!