The new state-of-the-art, extra-wide, MINO Six-high Cold Rolling Mill installed at Profilglass’ plant in Fano, on Italy’s Adriatic (east) coast, is in full production.
Through this new investment, Profilglass is aiming at serving the most highly demanding industrial sectors (including car, construction and shipyard industry) with top quality aluminium alloy strip of AA1xxx, AA2xxx, AA3xxx, AA4xxx, AA5xxx and AA6xxx, up to the maximum widths today required by such markets.
The new Six-high Mill for Profilglass has an impressive barrel length of 2500 mm, thus being capable of rolling aluminium alloy strip having a very wide maximum width of 2350 mm, down to a minimum gauge of 0.2 mm.
Beside being the biggest Cold Rolling Mill for aluminium running in Italy, it is also one of the biggest in Europe.
The new Six-high Mill is of state-of-the-art design and includes entry side trimmer & scrap chopper, EDT pass capabilities, off-line entry coil preparation system, off-line exit coil inspection system, automatic spool transfer device, most advanced AGC/AFC controls and powerful medium voltage AC main drives.
The Mill stand is equipped with MINO’s long stroke shifting system for the intermediate rolls, allowing a huge range of different products to be rolled successfully, coping with large variations in product’s widths and mechanical characteristics.
MINO has addressed the problem of heat build-up in the coils following subsequent rolling passes, by replacing the traditional coil transfer carrousel (floor mounted, pallet type) with a “High Bay” automatic coil storage System, fully integrated with the Mill, having a capacity of 400 coils. The High Bay automatic coil storage System has been designed and supplied by MINO together with the Mill, as a complete package.
An innovative characteristic of MINO’s High Bay System is that the automatic tracking of the coils and their transfer through the cold rolling process is fully integrated with the Mill’s level 2 automation, where the “recipes” for each product are fulfilled not only in terms of rolling mill set-up, but also in terms of coil handling, coil tracking and cooling time between passes.
Key data of the new Six-high Mill:
Type of alloys:
Max. Strip Width:
Max. Entry Strip Thickness:
Min. Exit Strip Thickness:
Max. Coil Weight:
Max. Coil Outer Diameter:
AA1xxx, AA2xxx, AA3xxx, AA4xxx, AA5xxx and AA6xxx series alloys
2350 mm
10.0 mm
0.2 mm
23 t
2200 mm
MINO is particularly proud of the consolidated and long-lasting partnership established with this Customer back in 2001 (when Profilglass awarded to MINO the first Contract for the supply of a Cold Mill) and which has continued uninterrupted through the years, following the spectacular growth of Profilglass in the aluminium strip sector.
Until today, MINO can boast of having installed, or being in the process of commissioning, the following impressive list of equipment for Profilglass:
- two Slab Scalpers, the second one capable of scalping 2800 mm wide slabs;
- two Hot Rolling Mills, the latest one becoming Italy’s biggest Hot Mill for aluminium, capable of transforming 2800 mm wide slabs into 25 t coils;
- four Cold Rolling Mills (!);
- a Continuous Annealing & Heat Treatment Line for automotive applications;
- a complete Continuous Tension Levelling, Cleaning & Passivation Line.
About Profilglass
Profilglass S,p.A, a company located in Fano, in the Marche region on the Adriatic coast of Italy, was founded in 1982 by Mr. Giancarlo Paci. Since its inception Profilglass has become the fastest growing Italian Company in the Aluminium rolling sector and one of MINO’s key clients.
The fact that the company grew in just a few years from 7.000 to over 300.000 m2 in factory area and from a mere 20 to now over 1.000 employees, provides an indication of its rapid growth. Today it produces close to 250.000 tonnes of aluminium products. With an impressive array of clients, it holds a leading position at international level, exporting to more than 85 countries worldwide.
Profilglass produces a very wide range of rolled products for diverse applications, including 3xxx strip for building applications, 6xxx strip for ABS (Auto Body Sheet, under the company name of LamiAl), circles for the cookware industry, tread plate including 5754 alloy, 5xxx plates for the shipyard industry, stucco coils, as well as spacers and decorative profiles for double glazing, a true trademark of Profilglass since its establishment (from which the Company’s name originates).
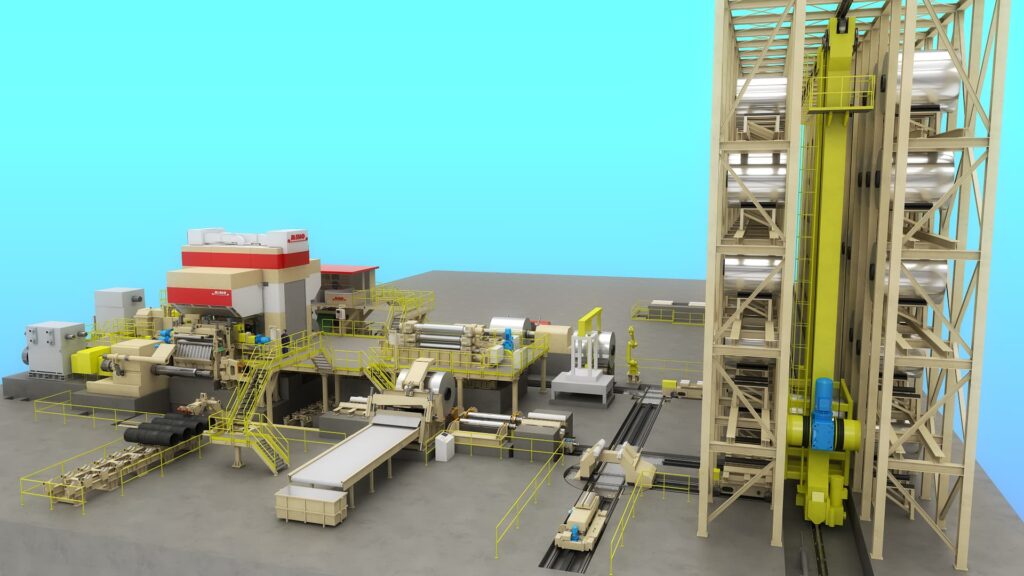
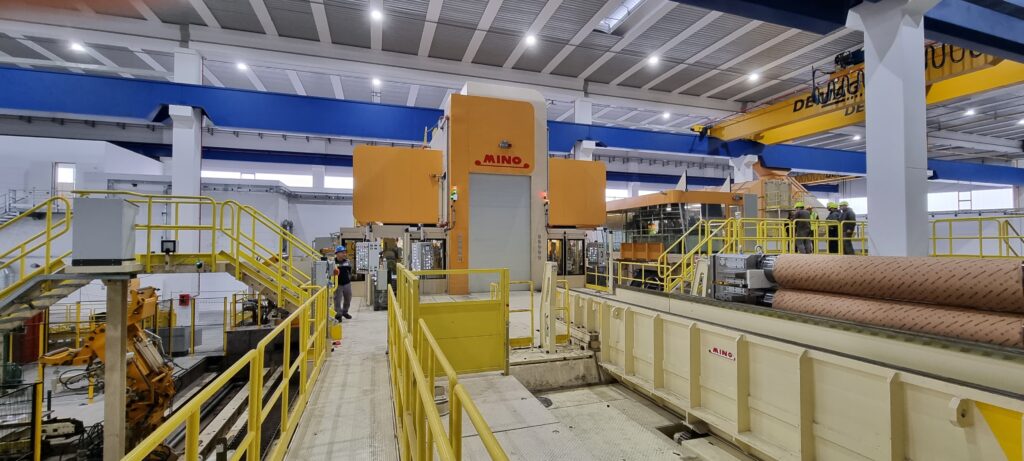
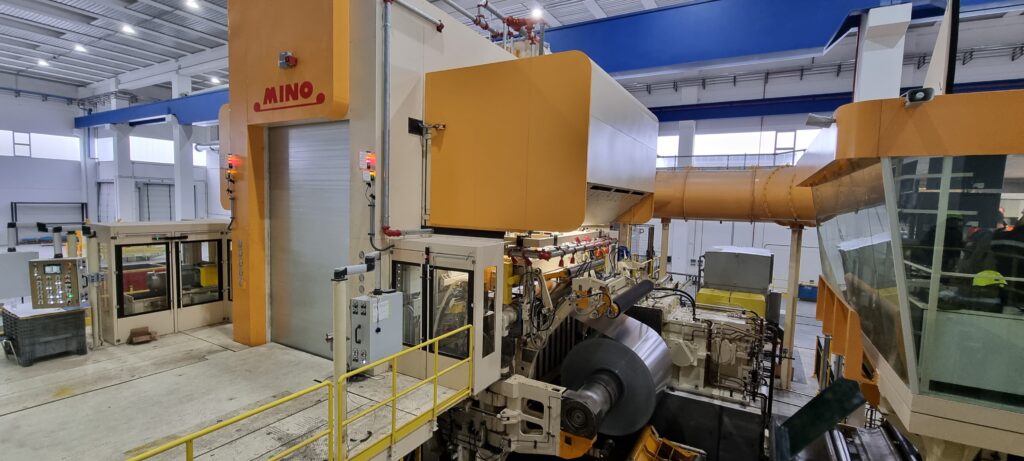