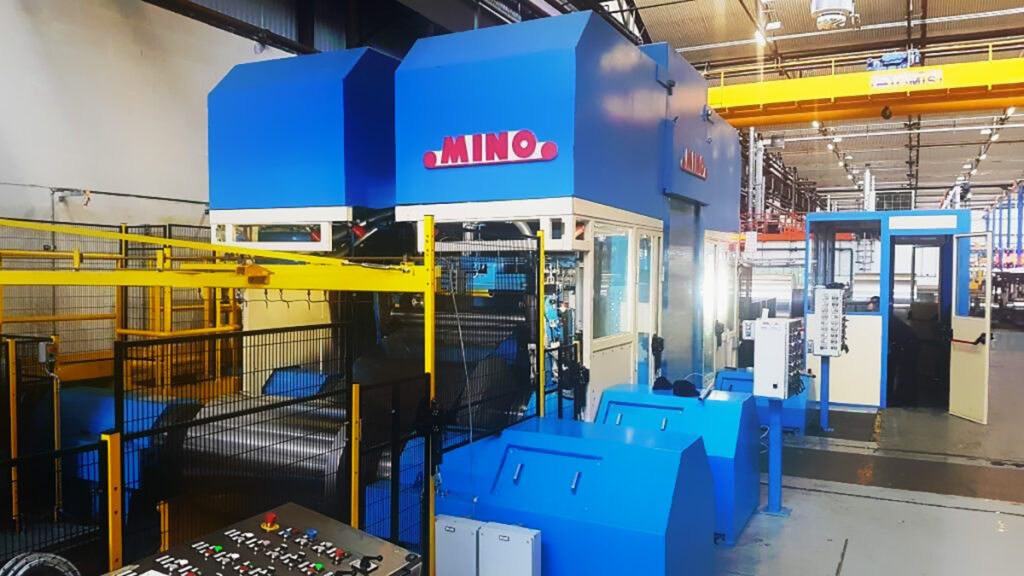
The state-of-the-art Battery Foil Finishing Mill at European Metals in Volpiano (TO) facilities located in northern Italy has achieved full production. This milestone comes two years after the contract was signed in 2022.
This strategic and far-sighted investment establishes European Metals as Italy’s first producer of battery foil and one of the pioneering players in this fast-growing sector across Europe.
This Battery Foil Mill is part of a brownfield project aimed at bringing back to full production and to the former glory the old Comital factory site.
To expedite the restart, the Battery Foil Mill was expressly designed to re-utilize the existing foundation, thus reducing the need for extensive civil works.
With a barrel length of 1500 mm, the Battery Foil Mill produces high-quality aluminium alloy strips with a final thickness of 12 µm and a bright-bright finish, catering to the demands of today’s battery foil market.
Alternatively, the Foil Mill is also able to serve the traditional household foil market (thus producing strip as thin as 2×0.0006 mm), where DingSheng Aluminium is well established as a global market player.
The Mill is designed with specific details to contain the fumes and the coolant carry over, critical for achieving the highest wettability levels required by the downstream battery process, equal or more than 33 dyn/cm.
A sophisticated exit blow-off system, paired with a high-efficiency fumes suction system has been rooted in the Mill’s design.
Even though the Mill is designed to be optimized for the battery foil application, still it retains a high degree of versatility with two uncoilers and an entry side trimmer with a dedicated suction system, thus enabling the possibility of online doubling.
Strip flatness is accurately controlled by the advanced AVANTITM TCS system for AGC/AFC control. This system, developed in-house by MINO Process Control team of experienced engineers, boasts numerous successful installations worldwide establishing a solid reputation for effectiveness and reliability.
In line with MINO’s standard operating procedures, the machine was fully designed in 3D, with meticulous attention to details from the outset.
This approach enables a perfect integration of a modern firefighting system to enhance Mill’s safety and optimizes the maintainability of the Mill itself maximizing the productivity.
After a smooth cold and hot commissioning, the Mill underwent an extensive and thorough tuning phase, resulting in successful production of battery foil.
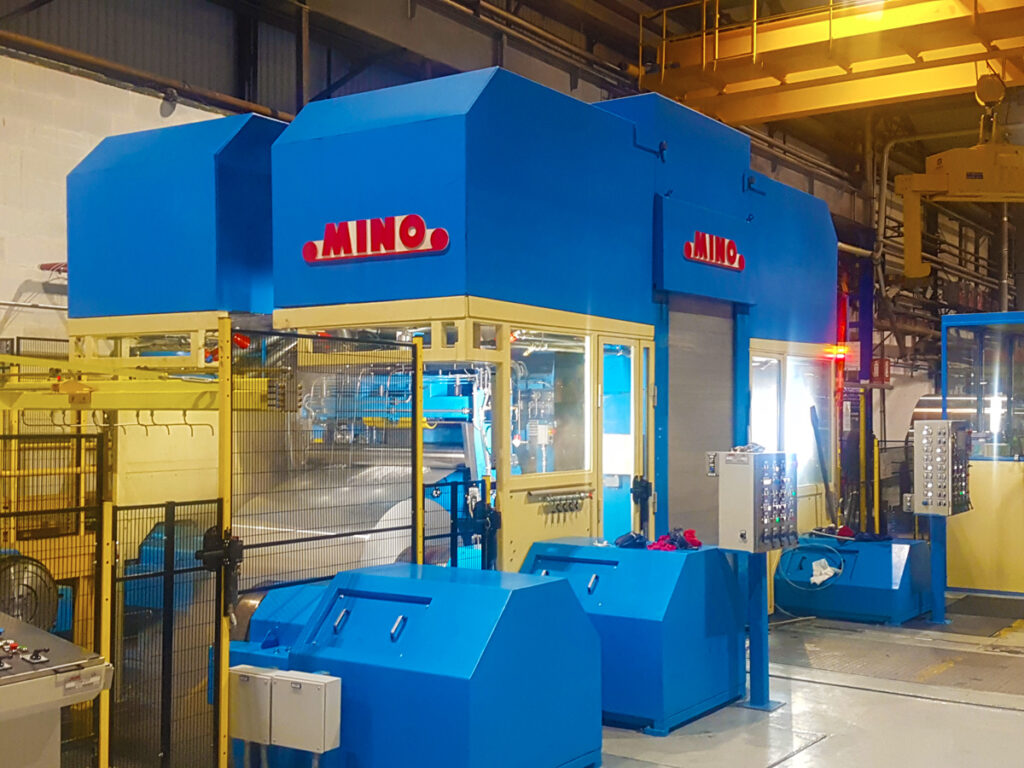
Type of alloys:
Max. Entry Strip Width:
Max. Entry Strip Thickness:
Min. Exit Strip Thickness:
Max. Coil Weight:
Max. Coil Outer Diameter:
AA1xxx and AA8xxx series alloys
1500 mm
0.70 mm
1×0.012 mm or 2×0.006 mm
8.5 t
1810 mm
MINO is particularly proud to contribute to European Metals’ success in the industry and to consolidate the enduring relationship with DingSheng Aluminium, which began back in 2010.
The partnership started in China with the installation of a massive Three Stands Hot Tandem Mill installed downstream of a Twin Belt Caster supplied by Hazelett.
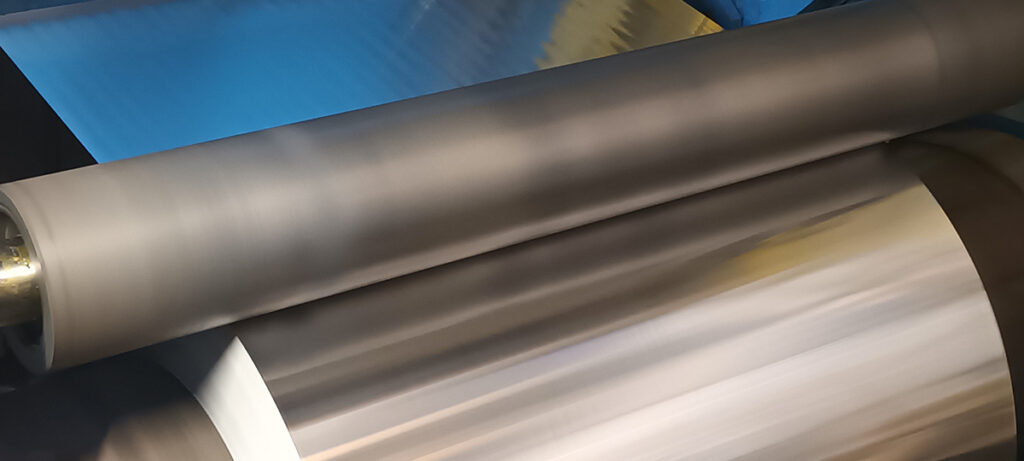
About European Metals S.r.l and Dingsheng
European Metals entered the European aluminium market in 2020 aiming at becoming a major player in Europe’s thin foil market, consolidating its presence in the household foil and foil package sectors, as well as in the fast-growing battery foil’s market.
This strategic direction followed the plant acquisition by Jiangsu Dingsheng New Materials Joint-stock Co.,Ltd., the world’s largest producer of aluminium foil and strip.
A massive renovation was undertaken at the historic production site in Volpiano (Turin, Italy) originally established in the 50’s.
In 2023, the company expanded further by integrating into the group Slim Aluminium, which operates two plants in Cisterna di Latina (Italy) and Merseburg (Germany).