Founded in 1923, Laminazione Sottile belongs to the Laminazione Sottile Group, which covers the production and transformation of aluminium, together with four other sister companies: Italcoat, Contital, IPS Industrial Packaging Solution (in Italy) and i2r Ltd. (in the UK, Korea and USA) and latest Contital LM (in Turkey) and PLLANA Gmbh (in Germany).
The Group’s companies work in an integrated production chain and manufacture rolled aluminium products in different alloys, dimensions and superficial treatments, including lacquering and printing, and aluminium food trays.
Through these inter-related companies, the Laminazione Sottile Group has the capability to supply the market with a wide range of rolled products for diverse applications such as packaging, HVAC-R, automotive, cookware and building, as well as with lacquered, laminated or printed products, semi-rigid aluminium foil containers, A-PET containers, aluminium rolls, cling film and oven papers for food packaging.
With a net production exceeding 120.000 tons per year, Laminazione Sottile is the Italian leading Company in the field of thin gauge rolled aluminium products, capable of supplying aluminium coils, sheets and circles in different alloys and dimensions, with gauges ranging from 6 mm down to 6 microns.
Following the very successful commissioning of the previous MINO Foil Finishing Mill that was completed in 2019, on June 2021 Laminazione Sottile decided to award a new Contract to MINO for the supply of one more set of MINO Foil Finishing Mill.
This new MINO Finishing Foil Mill will be the third MINO Foil Mill installed in the Company’s production facility located in Caserta, close to Naples, in the south of Italy.
With this latest addition, the Caserta plant will display a long list of equipment supplied by MINO during more than 20 year time span:
- a Cold Mill supplied in 1980 and recently refurbished by MINO with new process control system;
- a Foil Roughing Mill (MINO Foil Mill N.1) supplied in 1983;
- a massive Hot Mill with twin coilers, supplied in 1998;
- the latest Cold Mill commissioned in 2015;
- MINO Foil Finishing Mill (MINO Foil Mill N.2) commissioned in 2019;
- latest MINO Foil Finishing Mill (MINO Foil Mill N.3) to be installed in 2022.
Following the signature of this latest Contract, Mr. Cesare Pettazzi, President of MINO S.p.A. declared:
MINO is particularly proud and enthusiastic of such a consolidated and long-lasting partnership with Laminazione Sottile, that is a tangible evidence of the level of mutual trust developed by the two Companies during all these years. I believe that such a long lasting cooperation, which covers the whole spectrum of rolling equipment ranging from hot rolling to foil rolling, is outstanding and quite unique in the worldwide panorama of aluminium rolling.
Mr. Massimo Moschini, Chairman of Laminazione Sottile, declared:
The long lasting cooperation between Laminazione Sottile and MINO was built over nearly 40 years of projects undertaken together. Both parties worked hard with the aim at replacing the traditional Seller/Buyer relationship with a cooperation relationship based on mutual technical trust and good understanding of the respective needs. This is achieved with frequent and deep technical exchanges between the two companies’ technical teams. Project after project we have set the bar higher for MINO in terms of smart design, performance and equipment efficiency. The working system has proven to be fruitful so far, with MINO responding well to our requests. We trust that we will achieve together even higher goals
MINO Foil Mill N.3 will be very similar to MINO Foil Mill N.2, with just few “tweaks”, such as the edge control system by hot sprays being replaced by an induction pad system.
MINO Foil Mill N.3 is of high-speed design and includes two sets of pay-off reels for strip doubling, electro/mechanical solutions allowing for tension control at reels over an extremely broad range, automatic spool transfer device, side trimmer, state-of-the-art sensors & instruments, most advanced controls and AC drives.
To control the Mill at the high speeds demanded for this process, MINO will supply process controls incorporating the latest generation of AVANTItm TCS system for AGC/AFC control, including model based predictive control and a furtherly optimized function for automatic acceleration ramp.
The system is developed by MINO’s sister Company “MINO Process Control Ltd.” based in the UK, which specializes in the development and commissioning of most advanced process controls for thin gauge rolling.
The Mill’s design and automation system is being developed in compliance with the Industry 4.0 guidelines, such as advanced process control and monitoring systems, friendly man/machine interface, interactions between different machines (interoperability), intelligent maintenance system, remote diagnostics.
The final goal is to achieve high percentage in the Overall Equipment Effectiveness (OEE) and to improve the equipment reliability and operational safety.
The Mill is currently under design/manufacturing in MINO’s facilities in Alessandria, Vicenza and Wimborne (UK).
Key data of MINO Foil Mill N.3:
Type of Alloys:
Max. Entry Strip Width:
Max. Entry Strip Thickness:
Min. Exit Strip Thickness:
Max. Coil Weight:
Max. Rolling Speed:
Max. Coiling Speed:
AA1XXX, AA3XXX, AA5XXX, AA8XXX series alloys
1750 mm
0.75 mm
2 x 0.006 mm
14 t
1800 m/min.
2250 m/min
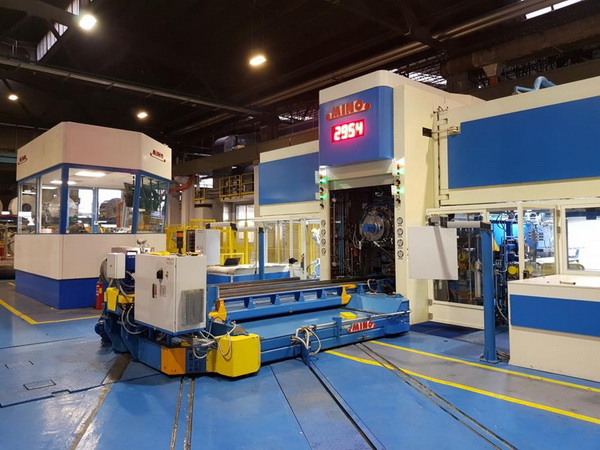